The raw powder packaging machine can automatically complete the whole process of bag making, measuring, filling, sealing, printing batch number, cutting and tearing, cutting, counting and other packaging processes. The packing speed and bag making length can be adjusted steplessly within the rated range without changing parts.
Common faults and solutions of raw powder packaging machine:
1. If the setting pulse cannot be transmitted to the electrical control cabinet or the material is not cut, it may be caused by the high sensitivity of the photoelectric switch or being blocked. At this time, please adjust the sensitivity of the photoelectric switch to an appropriate position or remove the blocker.
2. The number of pulses increases, but the actual weight decreases. After feeding, the actual weight is out of tolerance. This is caused by the large difference in the material level in the hopper. After adjusting a few bags, it can return to normal. Therefore, it is necessary to reasonably control the material level in the hopper (manual feeding) or adjust the number of preset bags (automatic feeding).
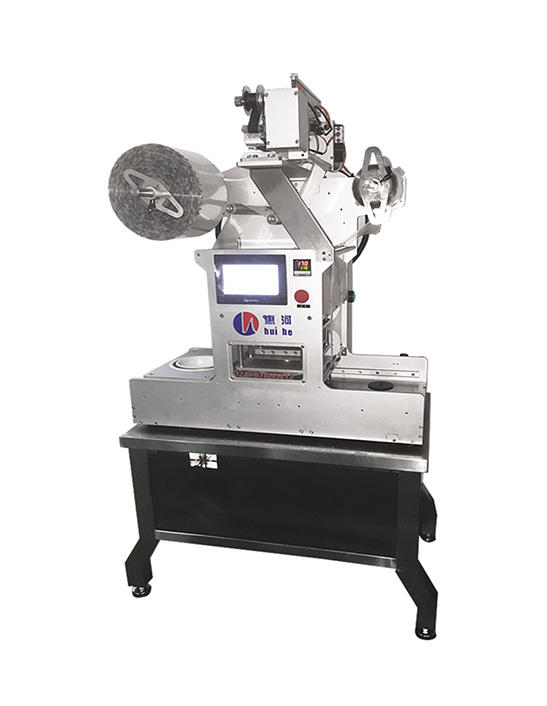
3. If the zero point instability (zero drift) of the calibration scale occurs, there may be a large airflow (such as wind, fan, air conditioner) or vibration source nearby; in addition, if the ambient humidity is high and the circuit board is damp, this phenomenon will also occur. At this time, please carefully remove the electronic scale shell, and use a hair dryer to drive off the moisture. Note: the hair dryer should not be too close to the circuit board, and should not be heated in a certain place for a long time to drive away moisture, so as not to damage the components.
4. If the screw does not rotate (that is, the stepping motor is blocked) or the measurement is good or bad, it may be that there are debris in the material that cause excessive resistance or the material cup is eccentric. In this case, please turn off the power and unload Unload the cup, remove the sundries or adjust the position of the cup. The operator can press the bottom of the container against the outlet of the material cup and change the operation method.
5. The measurement is inaccurate after changing the packaging specifications or materials. It may be that the position of the agitator scraper is not suitable. It needs to be adjusted so that the lower end of the scraper is about 10-15mm away from the screw. If there is leakage after filling, add anti-leakage net.